Operational Excellence - Lean Six Sigma
This is a one day programme to enable participants to contribute to business improvement and problem solving activities at work. The focus is a few simple but effective proven models and tools that can be used in dealing with the vast majority of business issues, whether they be in a shop floor or office environment.
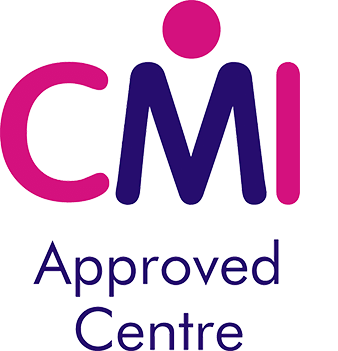
Course Overview
This one-day workshop will provide you with the tools and techniques to start implementing a structured programme of Waste Reduction, Productivity Improvement , Process Improvement and Problem Solving within a LEAN 6 Sigma format that has become the de facto standard for any organisation on the journey to Operational Excellence.
Designed to meet the needs of anyone involved in making their organisation more efficient and more effective, this workshop will allow you to focus on improving personal and business performance with tools and techniques used by high performing organisations around the world
What You Will Learn
- Lean Fundamentals – how to identify the 8 wastes of Lean thinking
- Six Sigma Fundamentals – what is Six Sigma and why it drive performance improvement
- Waste and Non-Value-Added Activity – erode profit you will learn how to identify, measure and plan to eliminate both
- 5S – The most used Lean tool, reduces waste, reduces variation and improves productivity
- DMAIC Methodology – the six-sigma route to improvement projects management – Define – Measure – Analyse - Improve - Control
- SIPOC – quickly identify the end-to-end components of any process
- Root Cause Analysis Tools – sometimes an issue is just a symptom of the real problem, the root cause needs to be identified before it can remedied.
- Leader Standard Work – the routines, skills and tasks that drive consistency and efficiency in the drive for continual improvement
This workshop is highly interactive, during the day you will get the chance to explore the opportunities for improvement in your own organisation as well as putting learning into practice in a safe environment. . At the end of the day you will also have templates and instructions to help you and your colleagues translate your learning into actions.
Who Should Attend
The staff, team leaders and first line managers of operational and service teams both on the shop floor and in the office. The intention is to provide delegates with the skills, knowledge and tools to make a real difference in their area of work and responsibility.
Course Tutors
Mike Epton - Business Consultant, Coach and trainer.
Mike is a Certified Lean Six Sigma Black Belt and Chartered Manager who has been using Lean Six Sigma tools and techniques since the 1980’s when he was part of a team implementing J.I.T Manufacturing, Kaizen and Total Quality Management at Thorn EMI, he has since been a Director of other large businesses, owned SME company’s and this year celebrates 21 years as an independent business consultant.
Trevor Durant - Business Consultant, Coach and trainer.
Trevor is a highly experienced Lean Six Sigma Black Belt with over 25 years of expertise in manufacturing, spanning a range of industries, including FMCG, brewing, food, confectionery, and textiles. Throughout his career, he has successfully led numerous improvement initiatives, delivering measurable results in efficiency, quality, and cost reduction. Before becoming a business consultant and trainer, Trevor held Director roles in manufacturing businesses where he was responsible for implementing all elements of a Lean Six Sigma programme.
Upcoming Locations & Dates
This course is provided on an in-house basis to suit individual clients.
Call us on 07733 107238 or email enquiries@cmbd.org.uk
Ready to find out more?
For more information on coaching, consultancy, training programmes, courses or our bespoke training service, please get in touch.